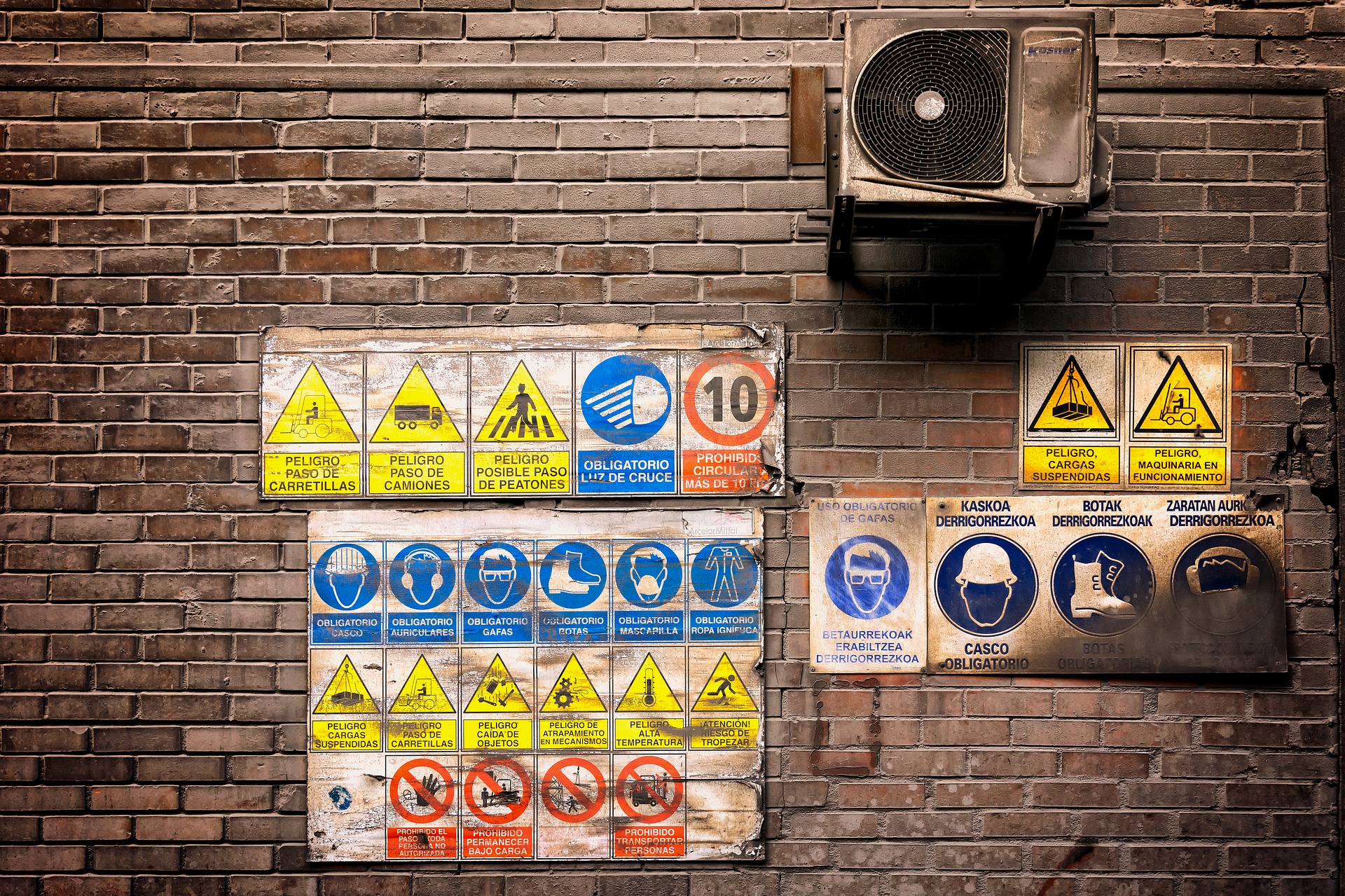
Cet article est issu du Blog des experts de Actu Environnement.
L’approche numérique de l’industrie se décline dans tous les secteurs et laisse entrevoir de nombreux bénéfices : anticipation, aide à la décision, performances accrues. La gestion des risques n’y échappe pas selon Armand Gilly, de la société Ealico.
L’industrie 4.0 fait beaucoup parler d’elle. Elle promet de réinventer l’ensemble des processus de l’entreprise grâce à la transformation digitale. Dans ce contexte, la maîtrise des risques industriels évolue et devient plus simple, plus fiable et prédictive. Les responsables techniques et HSE (Hygiène Sécurité et Environnement) sont les premiers concernés par ce phénomène. Cloud computing, LegalTech, Cobotique, internet des objets, intelligence artificielle et deep learning sont au programme.
Maîtriser les risques, pourquoi est-ce si compliqué sans le numérique ?
Les risques sont nombreux sur un site industriel. Pour se prémunir de ces risques et garantir la santé et la sécurité des travailleurs, ainsi que la protection de l’environnement, des réglementations ont été rédigées et définissent un cadre. En France, entre le Code de l’environnement, les arrêtés ministériels et les arrêtés préfectoraux, un site industriel est soumis à plus de 400.000 textes. Ces textes comportent chacun de nombreuses exigences et évoluent régulièrement. On compte en moyenne 25.000 évolutions par an.
Pour suivre cette complexité, des outils de veille réglementaire ont été créés. Ils complètent les textes officiels et permettent à leurs utilisateurs d’être informés des évolutions. Toutefois, ces outils ne suffisent pas. Après avoir pris conscience des nombreuses obligations réglementaires à suivre, il faut encore les comprendre, déterminer leur impact et suivre les évolutions réglementaires en permanence.
Aujourd’hui encore, 14 % des inspections de la direction régionale de l’environnement, de l’aménagement et du logement (Dreal) débouchent sur une mise en demeure suite à une non-conformité. Ces non-conformités peuvent provoquer des accidents, entraîner des pénalités financières, mais aussi des arrêts de production. En 2018, il y a eu 1.036 incidents et accidents déclarés par les exploitants de sites classés pour la protection de l’environnement (ICPE), soit en moyenne trois par jour.
Digitalisation : un quotidien simplifié et plus d’efficacité HSE
Bien que le risque industriel « zéro » n’existe pas, le respect strict des réglementations permet de s’appuyer sur un cadre sécuritaire qui a été éprouvé empiriquement. Les nouvelles technologies permettent d’agir dans ce cadre en simplifiant le quotidien des responsables techniques et HSE, ainsi qu’en facilitant la collaboration entre différentes parties prenantes.
Parmi elles, le cloud computing est en quelque sorte la colonne vertébrale de l’industrie 4.0 puisqu’il devient possible de disposer de l’information, n’importe où, et d’interagir entre différents systèmes. Dans la maîtrise des risques, le cloud est un élément central. C’est l’outil qui va permettre d’harmoniser les données, de fiabiliser les process et d’obtenir un accompagnement par des expertises externalisées de manière totalement digitalisée.
Des entreprises se sont spécialisées dans ce domaine, aussi appelé LegalTech, et simplifient l’usage des réglementations. Désormais, des algorithmes peuvent faire correspondre la part des textes réglementaires qui concerne directement des réalités industrielles de terrain spécifiques. Les personnes en charge du suivi réglementaire vivent une expérience simple et intuitive.
Les industriels qui gèrent leur suivi réglementaire de cette manière obtiennent des résultats immédiats : gain de temps, économie sur les arrêts de production et sur les inspections, fiabilisation du budget attribué à la conformité et montée en compétence des équipes.
La cobotique peut être un bon outil pour limiter les risques sur la santé et la sécurité au travail. Ce domaine vise à améliorer la collaboration homme-robot et peut-être une réponse aux travaux pénibles, dangereux ou à faible valeur ajoutée. Elle est notamment utilisée dans l’industrie pour manipuler des pièces, ou dans le nucléaire, pour intervenir dans des zones présentant de forts taux de radiation.
L’internet des objets (Internet of Things) est très lié au cloud computing. Il permet, en connectant les équipements industriels en ligne, d’en apprendre davantage sur leurs utilisations. Des capteurs intégrés permettent notamment d’anticiper tout dysfonctionnement.
Pour ce qui est de l’intelligence artificielle, les usages se trouveront surtout dans la prédiction avec le deep learning. Les algorithmes détermineront des tendances et pourront conseiller les utilisateurs sur les conséquences possibles de leurs décisions ou sur les actions à mettre en œuvre pour se prémunir de tout risque.
L’accompagnement quotidien grâce au cloud
Un autre avantage non négligeable à l’utilisation d’applications cloud est l’accompagnement que peuvent proposer les entreprises éditrices de la solution logicielle. Jusqu’à présent, les éditeurs créaient des logiciels qu’ils installaient sur les ordinateurs de l’entreprise cliente et ne proposaient que la maintenance et un support pour répondre aux problématiques informatiques.
Aujourd’hui, certaines entreprises sont à la fois des spécialistes informatiques et des spécialistes métiers. La frontière entre le logiciel et le service est plus poreuse. Elles proposent de bénéficier de leur expertise au quotidien d’une manière beaucoup plus efficace, en se basant sur les données des clients. La connaissance est partagée et chacun se concentre sur son cœur de métier. En externalisant une partie du suivi réglementaire à l’entreprise spécialisée, les industriels peuvent réaliser des économies conséquentes sur leurs charges fixes.
Les technologies énoncées ci-dessus sont d’ores et déjà opérationnelles. C’est sans doute le meilleur moment pour les industriels de repenser la maîtrise des risques de leur usine.
Avis d’expert proposé par Armand Gilly, directeur du développement de la société Ealico.