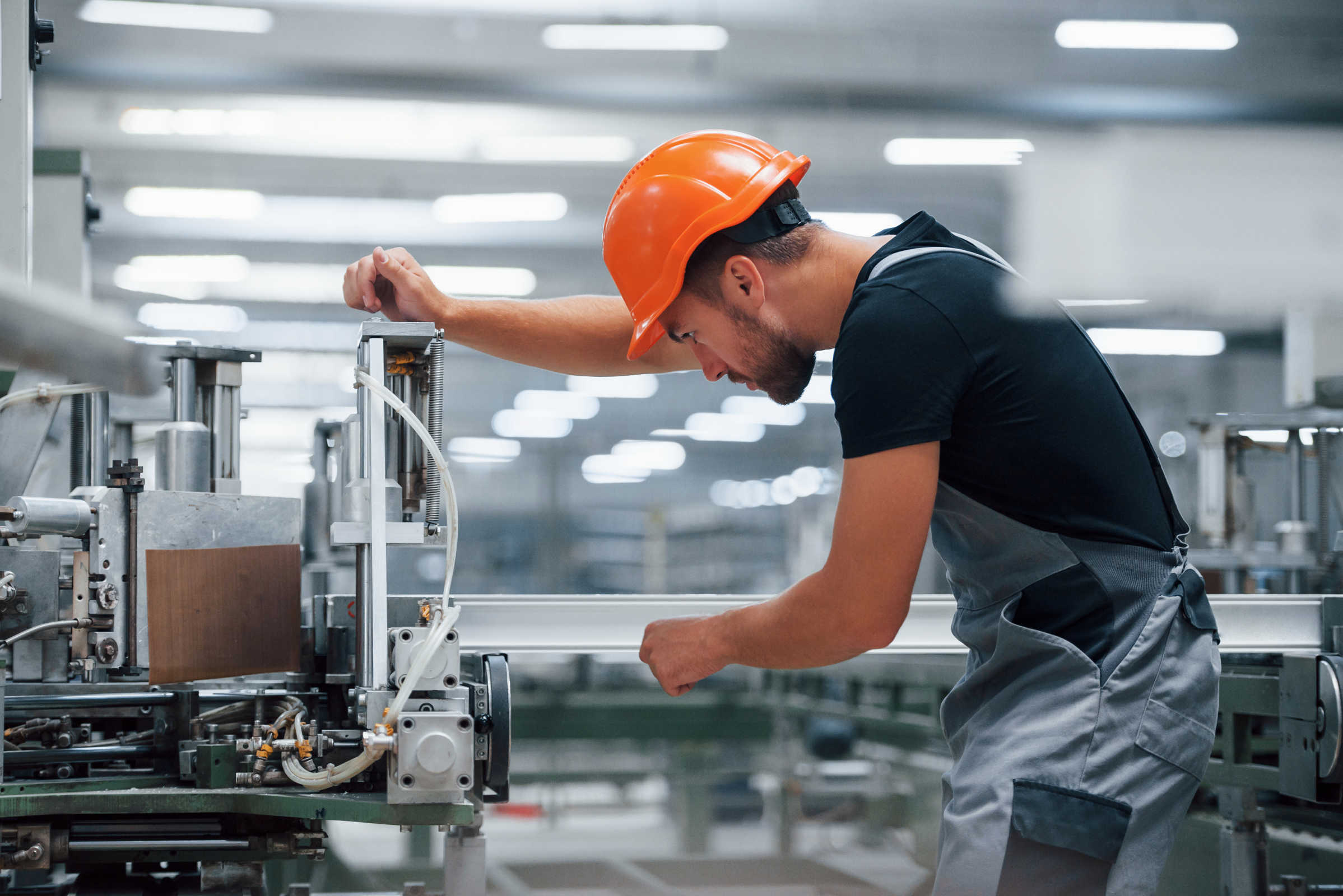
Article I = definition and benefits : TOTAL PRODUCTIVE MAINTENANCE
What is it and where does it come from?
Total Productive Maintenance is a method that originated in Japan in the 1970s. It focuses on the elimination of losses due to downtime, quality and accidents, which negatively influence the efficiency of the company. Nippondenso was the first Japanese manufacturer of automotive components to use TPM in 1961. Toyota and other Asian manufacturers soon deployed the approach in their organisations. It has since been adopted by many companies
In addition to improving productivity, this methodology considers that all employees of a facility should be involved in its maintenance, not just the team concerned. Indeed, for TPM to be effective, the full support of all teams is necessary.
And it works! Indeed, this participation helps to achieve the main objective which is: "To improve production volume, employee morale and job satisfaction".
Let's take a look at the direct benefits:
Improved maintenance and cleanliness of workplaces and their surroundings
Setting up a visual organisation
Elimination of time and material wastage
Improved monitoring of equipment
General improvement of the environment
Reduction of accidents at work
There is also a clear improvement in terms of behaviour, as it makes it possible to communicate and involve the whole company, which reinforces the positive attitude of employees through a sense of belonging
It also encourages staff to better respect collective rules.
Thus, the adoption of TPM means an overall improvement in productivity and employee safety.
But how does it work?
We will discover this in the next article dedicated to it as well as the key role that Matrix plays in the adoption of this methodology.