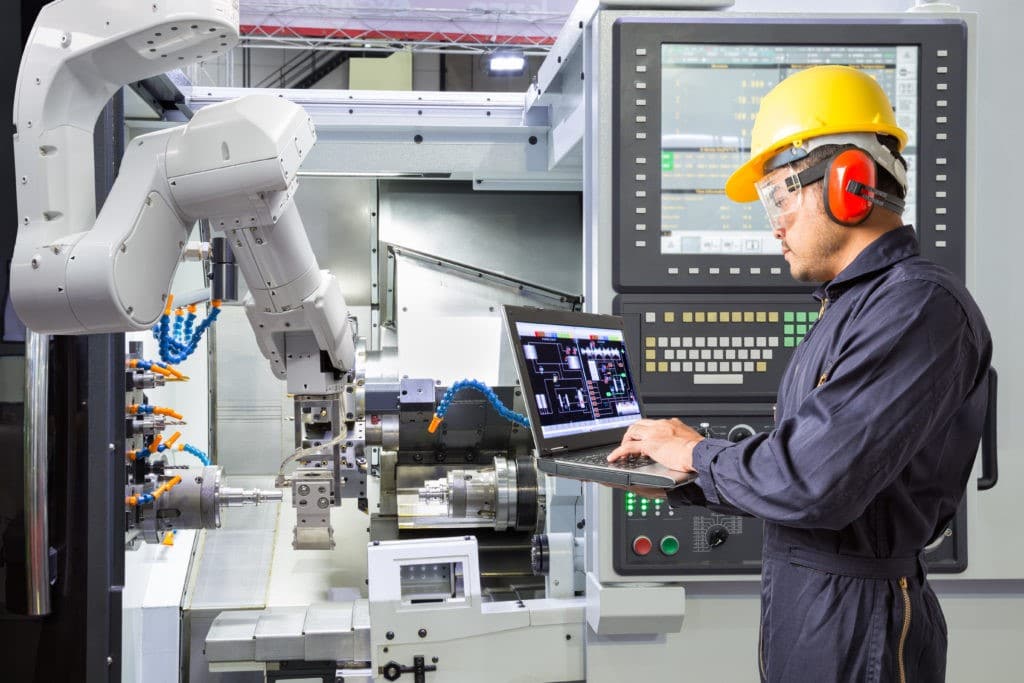
In a first article we mentioned Total Productive Maintenance and its advantages: an approach to equipment maintenance involving all the employees of a company, generally in small groups of activities, and which aims to obtain a perfect production process. This demand for the involvement of all members of the organisation is the main difference of this method, which was born in Japan in the 1970s
These objectives are achieved through the implementation of eight "pillars" aimed at establishing the reliability of the production process in order to maximize it
These 8 pillars of TPM focus on proactive and preventive maintenance techniques
Pillar 1: Case-by-case improvement or elimination of causes of loss.
Pillar 2: Autonomous maintenance or autonomous management of equipment.
Pillar 3: Planned maintenance.
Pillar 4: Improving knowledge and skills
Pillar 5: Control of product and equipment design.
Pillar 6: Quality control or maintenance
Pillar 7: Efficiency of functional services
Pillar 8: Safety, working conditions and environment
The deployment of a good TPM methodology is therefore based on the respect of these different disciplines, but also, above all, on the adoption of a good CMMS such as Matrix, which will allow the company to deploy an efficient TPM